ü In this new 20-hour on-demand course from AIAA and the Vertical Flight Society, the latest and greatest in eVTOL technology is presented.
ü All students will receive an AIAA Certificate of Completion at the end of the course
OVERVIEW
This multi-presenter course — featuring pioneering experts from industry and academia — provides an overview of the unique challenges and opportunities of this new class of vehicles. Both electric and hybrid-electric passenger carrying vertical flight aircraft are covered for a variety of missions ranging from personal/private use to urban air taxis to regional electric VTOL bizjets.
Also included is in-depth coverage of
industry-standard battery systems development (BAE Systems), advanced
high-power hybrid-electric hardware (LaunchPoint), PEM fuel cells and hydrogen
propulsion. In addition, the course includes fundamentals of vertical lift and rotor
aeromechanics, from design to state-of-the-art in acoustics.
(Course recorded live in 2023)
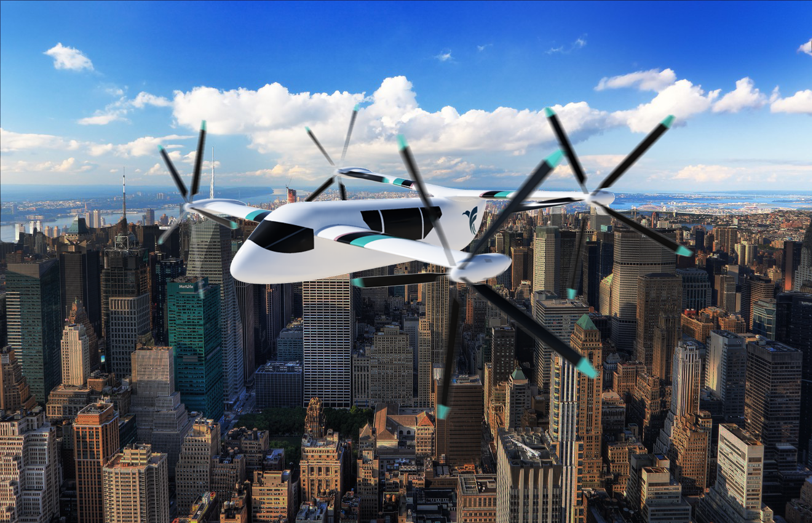
- The major constraints in designing an eVTOL aircraft, batteries and motors
- Leading battery chemistries, packaging, thermal management, charge/discharge, etc.
- Leading electric motor design types and metrics
- Acoustics fundamentals
- Sizing an eVTOL aircraft, batteries and motors for different missions and requirements
- Theory and available computational tools
- The pros and cons of different eVTOL aircraft configurations
- Cost estimating of eVTOL aircraft
Aerospace engineers interested in electric power. Electrical/mechanical engineers interested in VTOL aircraft. The content was presented in a simplified and practical manner to allow innovators, entrepreneurs, and non-VTOL experts to be able to make useful calculations and build their own design / simulation tools. The content is aimed at a wide audience of mixed aerospace and non-aerospace background. A simplified multi-rotor VTOL aircraft was designed and analyzed in class, progressively, as an illustrative example. In the final module, historical eVTOL design case studies were reviewed, as well as comparisons of the pros and cons of various eVTOL configurations.
All course slides and additional references will be available for immediate download. Stream the 20-hours of video recordings anytime, 24/7. No part of these materials may be reproduced, distributed, or transmitted, unless for course participants. All rights reserved.
CERTIFICATE
Receive an AIAA Course Completion Certificate upon viewing all course recordings. Please contact Lisa Le for a certificate.
COURSE FEES (Sign-In To Register)
- AIAA/VFS Member Price: $945 USD
- Non-Member Price: $1145 USD
- AIAA Student Member Price: $495 USD
---------------------------------------------
OUTLINE (Each module is approximately 4 hours total, and include exercises.)
Fundamentals:
Rotors, Aircraft, and Integrated Electric Power. Anubhav Datta, Associate
Professor, Alfred Gessow Rotorcraft Center, University of Maryland
Introduction - Why eVTOL? Why now? A brief history
- State-of-the-art in aircraft, battery, and motor
- Single vs. distributed propulsion
- Sizing an example eVTOL
- The connection to infrastructure
- Rotor aeromechanics
- VTOL aircraft
- Basic aerodynamics and performance
- Rotors vs. propellers vs. prop-rotors
- Coaxial and shrouded rotors
- Blade structural dynamics and loads
- eVTOL controls and trim
- Example Quadrotor and Tiltrotor
- Electric power
- Power architecture
- Brushless permanent magnet motors
- Engine-generator hybrid
- Lithium ion and Sulfur batteries
- PEM fuel cells and hydrogen storage
Sizing Advanced Battery Systems for eVTOL Application. Joshua Stewart, Principal Power Systems Engineer, BAE Systems
Describe battery operations and management
- Fundamentals of safe management and control
- Detail elements of battery packaging
- Discuss battery modeling
- Relate electrical and thermal elements to basic first principles
- Detail how systems are sized
- Assess battery performance (example)
- Power
- Energy
- Size
- Weight
- Life
- Cost
- Review development standards and testing
Brushless Permanent Magnet Machines and motor drives for Aircraft. Michael Ricci, LaunchPoint Electric Propulsion Solutions
Basic Permanent Magnet (PM) motor physics for aeronautical engineering - PM motor types and geometries (radial and axial flux)
- Motor performance metrics: size, weight, efficiency, torque, speed
- Characteristics and performance
- Designing a PM motor: sizing, weights and efficiencies
- Gearboxes
- Operating modes: motor vs generator
- Fundamental operation principles and sizing of motor drives
- Introduction to EMI concerns and mitigation
- Electric tail rotor example
eVTOL and UAM noise. James Baeder, Samuel P. Langley Distinguished Professor, Alfred Gessow Rotorcraft Center, University of Maryland
- Definitions
- Fundamentals of rotor acoustics
- Types of noise: broadband, rotational, and impulsive noise
- Ffowcs Williams and Hawkings Model
- Method to calculate noise
- Lifting-line versus CFD inputs
- Single versus multiple rotors
- Hover and forward flight
- Active control of noise
- Fundamental limits
- How quiet is quiet enough?
eVTOL Design and Analysis: Prof. James Wang, Director of the eVTOL Research and Innovation Centre, Nanyang Technical University, Singapore.
- Different configurations for VTOL
- Rotor designs and control methods
- How to quickly estimate performance
- Benchmark comparison of different eVTOL aircraft
- Design recommendations
- Cost estimation
- Vertiport operations
- Certification
INSTRUCTORS
Anubhav Datta is a member of
the Alfred Gessow Rotorcraft Center (AGRC) and an Associate Professor of
Aerospace Engineering at the University of Maryland at College Park. He
holds a M.S. and Ph.D. in Aerospace Engineering from Maryland. He re-joined
AGRC as faculty in 2016 after nine years at the U. S. Army Aviation Development
Directorate (ADD) at NASA Ames Research Center. At Maryland, Datta and his
students are focused on future vertical lift barriers through Mach-scale
wind-tunnel tests and HPC-based high-fidelity simulations. The research
conducted by Datta and his colleagues have led to new fields in VTOL such as
Mars Helicopter (2000), CFD/CA (2004), and eVTOL (2012). Over the years his
work has been recognized by the VFS Grover E. Bell and Alfred Gessow Awards, NASA
Technical Excellence in Publications Award, and U.S. Army and NASA Group
Achievement Awards. Datta is the founder and inaugural chair of the VFS eVTOL
Technical Committee, Chair of the AIAA Structural Dynamics Sub-committee on
Conferences, and Associate Editor of the Journal of the AHS.
Joshua Stewart is a Principal Power Systems Engineer at BAE Systems and a member of
the VFS. He has been working in the
aerospace industry for over 10 years.
Over the last 5 years, Josh has been a technical leader in the
development of high-power, high-voltage battery systems for aircraft propulsion
at BAE Systems. Josh is involved with the analysis and development of electric
and hybrid electric aircraft propulsion systems, including Li-Ion battery
storage, high-fidelity battery management systems, high voltage power
distribution, motor drives and cables.
He has played a critical role in the development of aircraft propulsion
solutions for CTOL and eVTOL aircraft.
With a strong background in flight-critical avionics and energy storage
for ground transit, Josh has been able to apply a broad systems approach to the
design of battery systems, including design for thermal runaway propagation and
containment. He holds a B.S. degree from
Binghamton University and a M.S. degree from Worcester Polytechnic Institute in
Mechanical Engineering.
Michael Ricci is the Vice President
of Engineering, LaunchPoint Technologies, and the driving force behind
LaunchPoint Technologies “Propulsion By Wire” electric aircraft propulsion
effort and spent the last 6 years as PI on a number of projects to develop
electric aircraft propulsion technologies. These projects have included
the development of highly efficient and powerful dual halbach array motors,
high specific power wide bandgap semiconductor motor drives, and
hybrid-electric gen-sets and bus power management systems. Applications have
included HALE vehicles, helicopter electric tail rotors, multi-rotors, and
eVTOL vehicles. During Mike’s 17 year tenure at LaunchPoint Technologies he has
worked on flywheel energy storage, implantable heart assist pumps, medical
oxygen concentrators, engine valve actuators, and a magnetically levitated
freight transportation system. Prior to joining LaunchPoint, Mr. Ricci worked
as a mechanical engineer with Spectra F/X, a theme park engineering company,
where he served as Project Engineer on several very large custom systems with
high cycle rates, intimate man-machine interfaces, and high human-safety
concerns.
James Baeder is a member of
the Alfred Gessow Rotorcraft Center as a Professor of Aerospace Engineering at
the University of Maryland at College Park. He is currently the Samuel P.
Langley Distinguished Professor at the National Institute for Aerospace. He
holds a M.S. and Ph.D. in Aeronautics and Astronautics from Stanford
University. He joined the AGRC in 1993 after nine years at AFDD. His research
interests are in developing and applying Computational Fluid Dynamic methods to
better understand rotor aerodynamics, acoustics and dynamics. He is a pioneer
in the development of high-fidelity CFD and aeroacoustic methods and tools for
rotorcraft. Currently he is focused on the development of improved CFD
algorithms on GPGPU technology, to: capture the details of laminar/turbulent
transition; dynamic stall; as well as tip vortex formation, convection and
interaction with other surfaces including fuselages, towers or the ground and
including adjoint capabilities. Dr. Baeder's research has been funded by
Excelon, NASA Ames and Langley, the Army Aeroflightdynamics Directorate, the
Army Research Office, the National Rotorcraft Technology Center, NAVAIR and
DARPA, with support from the various helicopter companies. Dr. Baeder is a
Technical Fellow of the Vertical Flight Society, member of the Acoustics
Technical Committee (1996-present), member of the Aerodynamics and Propulsion
Area Committee, and Chairs the Innovation and Commercialization Committee of
the Business Network for Offshore Wind as well as the National Offshore Wind
Innovation Center.
Dr. James Wang has over 30 years of
experience in aerospace and high-tech industries. He is an internationally
renowned expert in eVTOL aircraft and advanced air mobility. In 2013, WIRED
Magazine named Dr. Wang “The Steve Jobs of Rotorcraft” for his ability to think
“outside the box” and pushing the transportation technology boundaries for
inventing and designing the AgustaWestland Project Zero, the world’s first
all-electric VTOL technology demonstrator aircraft. Dr. Wang has held many
executive leadership positions, including as Senior Vice President of Marketing
and Vice President of R&D at Leonardo Helicopters; led Strategic Sales and
worked on numerous helicopter designs at Sikorsky Aircraft. He is the founder
of Vtolwerke LLC which provides consulting services in advanced air mobility,
eVTOL aircraft designing and problem solving, product development strategizing,
and due diligence studies. Dr. Wang is currently a full professor teaching
aircraft and eVTOL design.
Dr. Wang received his Bachelor’s degrees in Aeronautical & Astronautical Engineering and in Electrical Engineering & Computer Science from M.I.T., and a Master’s and PhD in Aerospace Engineering from the University of Maryland. After completing his PhD, Dr. Wang started his career at Sikorsky Aircraft, where he was known as one of the most energetic and prolific engineers and managers; he contributed greatly to the Comanche, Black Hawk, Naval Hawk, S-92 and the Variable Diameter Tiltrotor programs.
Classroom hours / CEUs: 20 classroom hours / 2.0 CEU/PDH
Contact: Please
contact Lisa Le or Customer Service if you have questions about the course or
group discounts (for 5+ participants).
Title | Credit(s) | |
---|---|---|
1 | ||
2 | ||
3 | ||
4 | ||
5 | ||
6 | ||
7 | ||
8 | ||
9 | ||
10 |