Instructor: Don Edberg, Professor of Aerospace Engineering at Cal Poly Pomona & Adjunct Lecturer, Astronautical Engineering, University of Southern California (USC)
ü This comprehensive course applies numerous engineering disciplines to the design & analysis of launch vehicles, including many practical applications not found elsewhere.
ü Course includes over 1,800 slides providing theory along with many illustrative application examples of existing or heritage hardware, and solved practice exercises to enhance the learning experience.
ü Based on the second edition of the instructor’s 1,070-page AIAA textbook “Design of Rockets and Space Launch Vehicles”
ü All students will
receive an AIAA Certificate of Completion at the end of the course.
OVERVIEW
This
course presents a comprehensive treatment of the fundamental principles
involved with the interdisciplinary design of launch vehicles. It is recommended
for anyone interested in an introduction to all the principles and aspects of
launch vehicle design and development, including engineers of all types – systems,
aerodynamics, controls, structures, dynamics, thermal analysis, propulsion,
reliability, manufacturing, as well as researchers, mission designers,
technical managers, and both undergraduate and graduate students. This course provides
a survey of the material in the instructor’s AIAA textbook “Design of
Rockets and Space Launch Vehicles” (2nd
edition, 2022), with additional
materials on current topics such as reusability and small launch vehicles.
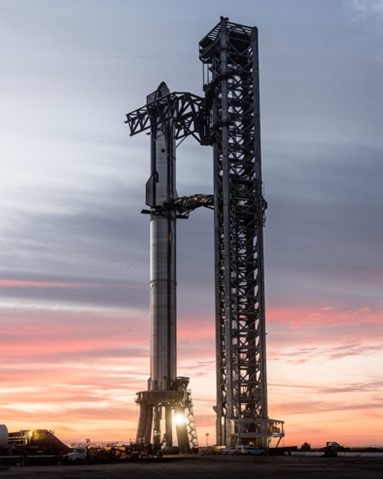
"WHAT YOU WILL LEARN: COURSE OUTLINE AND APPROXIMATE TOPIC SCHEDULE
Lecture |
Subject. (number) refers to chapter number in Design of Rockets and Space Launch Vehicles |
1 |
(1) Introduction to Launch vehicles (LVs). Anatomy of a LV, launch & ascent phases, worldwide launch sites. The global space economy, market & need for LVs. LV terminology & vocabulary. (2) Technical history of rocketry & LVs: early events, WWII, the Cold War, ICBMs. |
2 |
(2) History of LVs (cont.): moon race, space shuttle, oddities. Current LVs; future developments. (3) Mission requirements, top-level performance analysis for LVs. Orbits & trajectories: due east, direct orbits, polar, sun-synch, Molniya. LV design velocity estimation including gravity, drag, & other losses. Effects of launch site location. Ground launch vs. air drop, launch direction calculation, launch windows, orbit injection & shutdown conditions. |
3 |
(4) Propulsion: exhaust speed, mass flow, calculation of thrust & ∆v. Solid motors: grain, thrust profiles. Liquid engines: mixture ratios, performance vs. altitude, specific impulse, room-temp vs. cryogenic propellants, hypergolics. Engine thrust-to-weight ratio. Aerospike engines, hybrid rockets. Effective specific impulse during ascent. |
4 |
(5) Performance estimation using dimensional and dimensionless parameters of mass ratio and structural fraction. Three LV mass categories. SSTO & benefits of staging. Four types of staging, including series & parallel. Performance of series & parallel staging, optimization using Lagrange multipliers & “brute force” methods. All hydrogen Saturn V! Propellant crossfeeding. LV design sensitivities/trade-off ratios: where is the best place to improve performance? Recovery calculations: energy to dissipate, drag vs. propulsive recovery, flight profiles, additional propellant required, recovery system mass. |
5 |
(6) Flight through the atmosphere. Simplified LV equations of motion with aerodynamic lift & drag, gravity, buoyancy. Moving vehicle coordinate system, local horizon frame, pitch-plane trajectory simulation, gravity turns & other types of guidance. |
6 |
(6 cont.) LV trajectory optimization: Newton & 1st optimization problem. Conflict between gravity & drag/thermal loads. Importance of thrust-to-weight ratio. Lofting, other optimization techniques, optimization software (including public domain). Ten LV trajectory profiles:Falcon 9, Ariane, Delta III, Saturn I/V, Space Shuttle, others. (7)LV structures. Tank layouts, bulkheads, dome shapes, propellant feed line routing, toroidal tanks. Examples from Atlas, Delta, Saturn, Ariane, Zenit, & Shuttle. Multi-engine arrangements. Payload accommodations: payload fairings, payload attach fittings, including ridesharing. Types of structures:skin & stringer, sandwich, waffle/isogrid/orthogrid. Materials include metals (aluminum, Al-Li, steel), composites (graphite/epoxy). Material usage guides. |
7 |
(8) LV inboard profile. Propellant mass & volume calculation by ∆v & specific impulse including “real-life” additions for startup, ullage, thermal contraction. Sizing of tanks and domes including ullage and shrinkage, intertank/interstage structures, skirts, thrust structure. Two-stage-to-orbit (TSTO) vehicle sizing example. Engine selection: existing vs. “rubber” engines. Mass properties: calculation of center of mass & inertias when loaded, empty, after stage separation. |
8 |
(9) LV ground, transportation (handling/road/rail/ship/plane), & ascent loads: effective load from distributed loads, ground winds on pad, in-flight aerodynamic & inertial forces during trimmed flight at max-q. Why max-q and max-qa are important. Calculation of moments, shears, axial loads. Detailed Saturn V example. Load curve rules-of-thumb. Measuring atmospheric winds, Jimsphere. Load relief. (10) Stress terminology. Thin-wall cylinder stresses due to axial & bending loads. Tank positioning vs. increased tank mass. Reduced allowable stress due to structural stability/buckling. 7 ways to improve structural stability. Internal stresses induced from aero loads, internal & hydrostatic pressure, geysering. |
9 |
(10 cont.) Overall stress state & required wall thickness calculation for tanks, skirts, adapters, interstage. Simple rules for LV structures. Property variations with temperature. Table of selected material properties. (11) Launch environment: vibration, shock, acoustics, thermal loading. Engine startups & cutoffs. Explosive/ordnance & non-explosive separations. Payload fairing separation dynamics. Payload separation via clamp bands, pyro shocks. Acoustics: ignition overpressure, liftoff & max-air acoustics, acoustic suppression. Thermal environment from aero heating, plume radiation, protection systems. Payload structural design verification, coupled-loads analysis. Payload environment, acoustics, thermal; isolation. |
10 |
(12) Stability & Instabilities. Stability & control vs. guidance & navigation. Attitude determination. Stability & control: how to stabilize unstable vehicle. Flight control system elements. Thrust vector controlled (TVC) vehicle equations of motion in pitch plane. Tank positioning vs. stability and CG travel. LV block diagrams, transfer functions. Introduction to complex variables & root locus diagrams. Wind gust response. Instabilities from LV flexibility, “tail-wags-dog,” sloshing, pogo, resonant burn. |
11 |
(13) Manufacturing. Metal structures: conventional vs. friction-stir welding. Fabrication of tanks, connecting structure. Composite materials: layups, fabrication techniques. The future: 3D/additive printing, fiber placement. Production flow and LV stacking. (14) LV systems: onboard & launch pad facilities. Propellant loading & conditioning. Pressurization systems, hydraulics, thrust-vector control. Avionics, data systems, electrical, telemetry basics: transducers, data handling, multiplexing. Ordnance & non-pyrotechnic separation systems. Launch pad facilities: umbilicals, swing arms, propellant loading, lightning protection, vehicle hold-downs. Acoustic suppression. Examples from Saturn V, Shuttle, Falcon 9, others. Logistics/equipment needed for recovery & re-use of payload fairings, boosters, upper steps. |
12 |
(15) Testing: reasons for testing. Ground & flight wind tunnel, structure, pressure, vibration, shock, acoustic testing. Radio frequency/RF & software testing. Hot gas & plume testing. Redundancy, reliability, k-out-of-n system reliability with multi-engine examples. NASA Safety definitions. (16) Failures: examples & lessons learned. Most common failures, case studies. Five mistakes to look for. Failures of propulsion, structure, avionics/software systems. Flight termination systems, range safety. Abort trajectories, ascent shaping to avoid “black zones.” Best practices to avoid failures. (17) LV Financial analysis, project management, cost estimation. Design decision-making, cost engineering, cost-estimating relationships, inflation. Recommendations & Atlas V cost example. Software cost. Fallacy of “cost per pound” or “per kg”. Propellant costs. Economics of re-use. |
AUDIENCE
This
course is intended for engineers of all types – aerodynamics, controls,
structures, propulsion, reliability, manufacturing, systems, as well as
researchers, mission designers, technical managers, and both undergraduate and
graduate students, who want to enhance their understanding of the fundamental
principles of the design and operation of space launch vehicles. This
introductory course focuses on the basic physical concepts and mathematics utilized
in the preliminary design and analysis of launch vehicles including many
practical aspects not found elsewhere.
MATERIALS
- Course Notes: All slides will be available to view online in Aerospace Research Central (ARC).
- Course slides are also available for purchase in a bound printed version from Amazon (ISBN 9798848725438).
Lecture Recordings: Stream the 36 hours (12 recordings x 3 hours) of video recordings anytime, 24/7. No part of these materials may be reproduced, distributed, or transmitted, unless for course participants. All rights reserved.
COURSE
FEES (Sign-In to Register)
- AIAA Member Price: $1495 USD
- Non-Member Price: $1695 USD
- AIAA Student Member Price: $695 USD
"Awesome course, extremely instructive and full of very useful information that can be very difficult to find elsewhere."
INSTRUCTOR
AIAA
Associate Fellow and former Boeing Technical Fellow Don Edberg has taught
aerospace vehicle design since 2001 at California State Polytechnic University,
Pomona (CPP); he also holds part-time positions at USC and UCLA. He is co-author
of the course textbook Design of
Rockets and Space Launch Vehicles, published in 2020 with a 2nd
edition in 2022.CPP student design
teams he has advised have placed 1st, 2nd, or 3rd
over 20 times in AIAA student design competitions in Missile Systems, Space
Transportation Systems, Spacecraft Design, and Aircraft Design. At CPP, he has
received the Engineers’ Council
Distinguished Engineering Educator Achievement Award, the California State
University Wang Family Excellence in Teaching Award, Provost’s
Excellence in Teaching Award, College of Engineering’s Outstanding Teaching and Outstanding Advisor awards, and the
Northrop Grumman Faculty Teaching award. He has presented short courses
in launch vehicle and spacecraft design to several NASA centers, the National
Transportation Safety Board, U.S. Federal Aviation Administration, U.K. Civil
Aviation Authority, Northrop Grumman, Boeing Satellite Systems, and several
smaller aerospace businesses. He was a Technical Fellow at Boeing and
McDonnell Douglas, where he worked on R&D programs for launch and space
systems, authored or co-authored ten US patents, and received the Silver
Eagle award from McDonnell Douglas as Chief Engineer on the STABLE active
microgravity vibration isolation system that successfully flew on STS-73
shuttle mission. He has also worked at Convair, AeroVironment (where he was the
chief engineer on the electric-powered, back-packable FQM-151 Pointer UAV), JPL, NASA Ames, NASA
MSFC, and US Air Force Research Lab. He received a B.A. in Applied Mechanics
from UC San Diego, and M.S. and Ph.D. degrees in Aeronautical and Astronautical
Sciences from Stanford. He is an Eminent Engineer in Tau Beta Pi and was
Engineer of the Year of the AIAA Orange County, CA section.
Classroom hours / CEUs: 36 classroom hours / 3.6 CEU
Contact: Please contact Lisa Le or Customer Service if you have questions about the course or group discounts (for 5+ participants).
Title | Credit(s) | |
---|---|---|
1 | ||
2 | ||
3 | ||
4 | ||
5 | ||
6 | ||
7 | ||
8 | ||
9 | ||
10 |